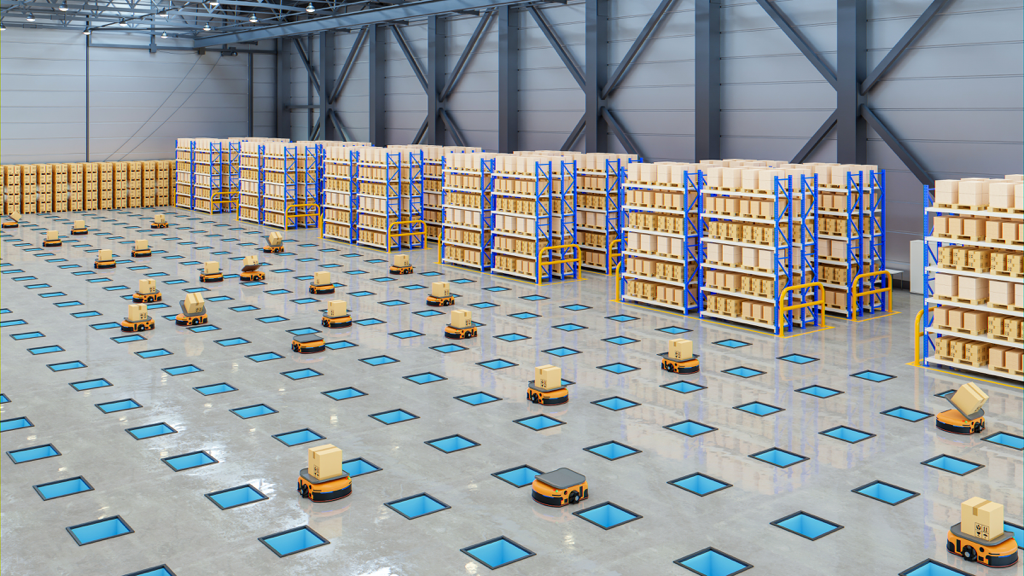
Robotics in Logistics
With the rapid growth of online orders and e-commerce, automating logistics and warehousing processes has become increasingly critical. Robotic automation can significantly reduce the time required to fulfill orders, enhance the productivity of warehouse employees, and ultimately improve customer satisfaction. As companies strive to meet rising demand, robotics offers a pathway to more efficient and reliable operations.
Two kinds of Robotics Technologies in warehouse automation
If you’re exploring robotic solutions to automate your warehousing processes, you’ll likely encounter Automated Guided Vehicles (AGVs) and Autonomous Mobile Robots (AMRs). These technologies, while sometimes used interchangeably, have distinct differences and advantages.
Automated Guided Vehicles (AGVs): AGVs are unmanned load carriers guided by software and sensor-based systems along predefined paths, similar to trains. They are ideal for transporting heavier payloads and performing repetitive tasks. AGVs are best suited for stable environments with consistent layouts, such as manufacturing facilities transporting bulk raw materials.
Autonomous Mobile Robots (AMRs): AMRs, in contrast, navigate using onboard sensors and maps, allowing them to choose different routes and avoid obstacles autonomously. They are highly adaptable to dynamic environments, making them suitable for complex warehouse operations like order picking and inventory management. AMRs can significantly reduce travel time within warehouses by bringing goods directly to workers, enhancing overall efficiency.
Mainstream Robotic Technologies in Warehousing and Logistics
Robotic technologies play a vital role in modern warehousing operations, offering various applications such as order picking, product putaway, and in-warehouse transfers. Here are some common robotic solutions:
- Robot-to-Goods Picking: AMRs travel to pick zones, where workers pick items and place them in totes carried by the robots. This method minimizes worker travel within the warehouse.
- Goods-to-Person Picking: AMRs transport items in totes or on moveable shelves to pick stations. Workers pick and scan items for shipping, significantly reducing the time spent walking.
- Follow-the-Robot Picking: AMRs act as intelligent picking carts, guiding workers through pick zones and improving batch density. This approach optimizes order fulfillment processes.
- Transit Robots: Robots transport completed totes or cartons to staging locations, reducing the need for manual transport and enhancing efficiency.
- Full Pallet Moves: Robots handle full-pallet putaway or replenishment, reducing the need for manual labor in these travel-intensive activities.
Implementing Robotic Technologies in Logistics
When implementing robotic technologies in logistics, several factors need to be considered:
- Initial Investment: The upfront costs of purchasing and integrating robotic systems, including training for employees, can be substantial.
- Environmental Adaptability: Different robots are suited to various environments. Selecting the appropriate navigation technology (e.g., magnetic, laser, or visual) is crucial based on the specific conditions of the warehouse.
- Data Integration: Ensuring that robotic systems seamlessly integrate with existing warehouse management systems (WMS) and enterprise resource planning (ERP) systems is essential for optimal performance through warehouse control systems (WCS).